
New method 3D prints glass at low temperatures
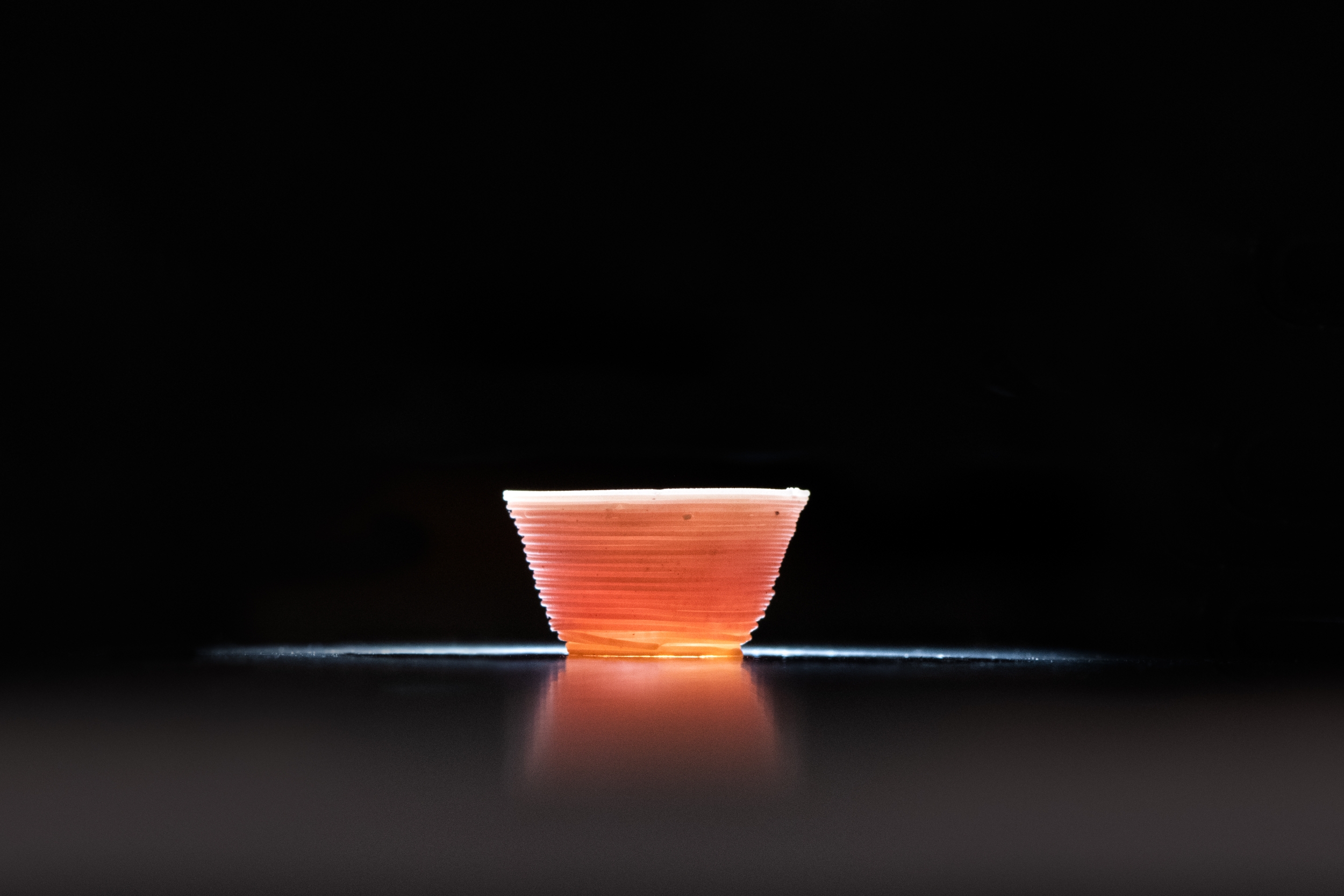
Glass is an important material in the creation of electronic components because of its insulating properties, stability, and wide availability. A new 3D-printing technique documented by researchers in Lincoln Laboratory's Advanced Materials and Microsystems Group now enables complex glass structures to be printed without heating the structure to high temperatures.
Past methods for 3D printing glass relied on a high-temperature processing step, generally greater than 1000°C, to create the final glass object. The method developed by Laboratory researchers can produce a stable glass structure without needing to expose the part to temperatures above 250°C. This capability can enable the material to be integrated with temperature-sensitive microelectronic components, which can be irreparably damaged above 400°C.
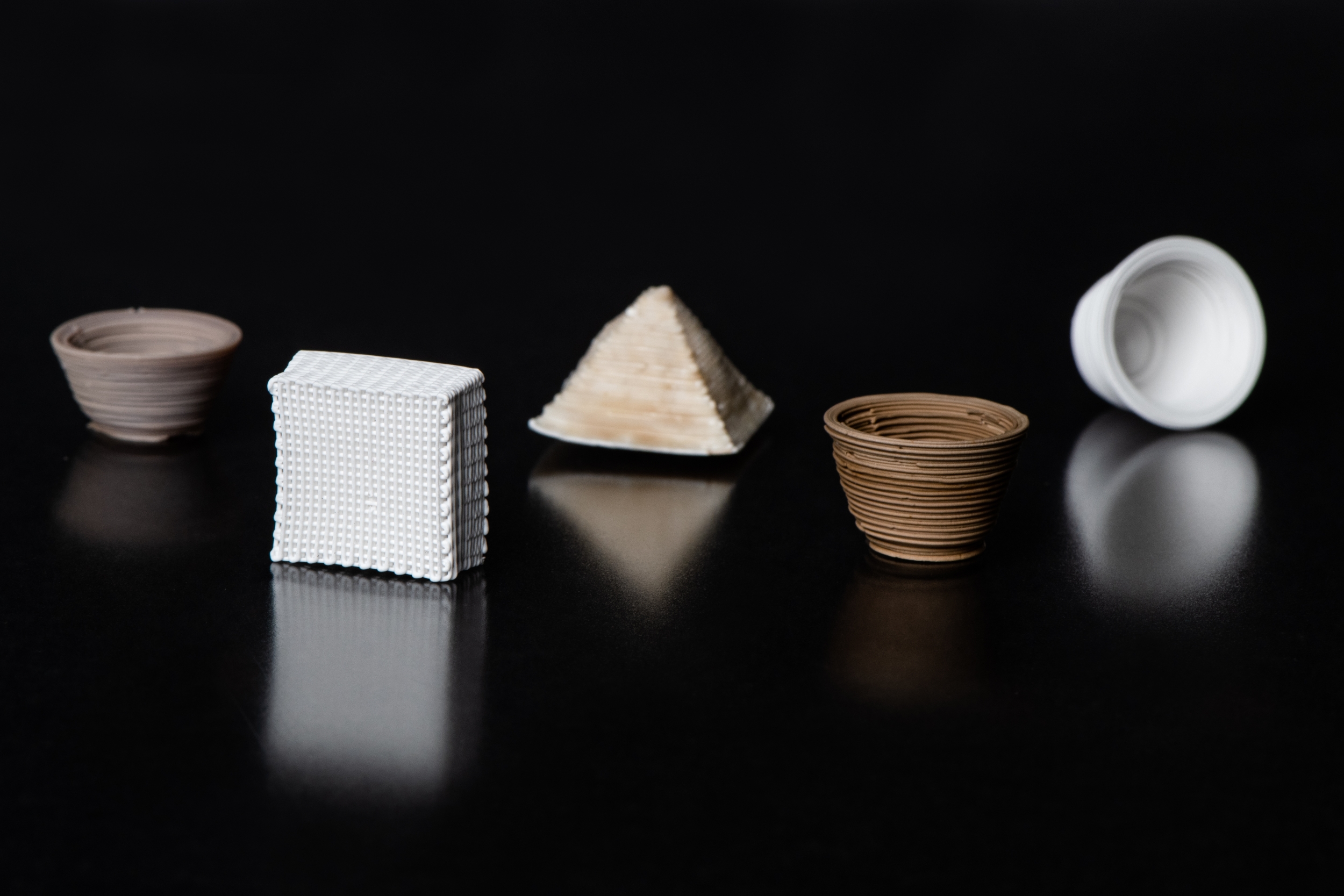
"Other techniques require heating the structure to the point where the microelectronic components would completely malfunction," says Bradley Duncan, who leads this work. "This 3D-glass system can be directly deposited onto existing electronics, and its properties more closely match silicon-based microelectronics."
Development of this technology began when researchers realized that their work creating thick glass film materials for silicon wafers could be adapted for use in 3D printers. Their goal was to create a material that had the properties of glass but could be processed like a polymer.
"While optimizing the processing conditions for forming thick films on silicon wafers, we discovered that by altering the formulation of the liquid precursor, we could produce a fluid that could be extruded in a filament form while also producing self-supporting structures," says Duncan.
Extruding the fluid in a filament form is key to adapting the material for use in a 3D printer, which has a precise nozzle that deposits, or prints, material onto a plate. After the printer has created one layer of the object, it adds more material on top of that layer to continue creating the object.
This glass method, which has a patent pending, is printed by using a special ink. The ink is made up of particle components and a "water glass" solution. After the part is printed and dries, it is submerged in a mineral oil bath to evaporate the water from the ink, causing the glass molecules and particle components to condense and harden into glass.
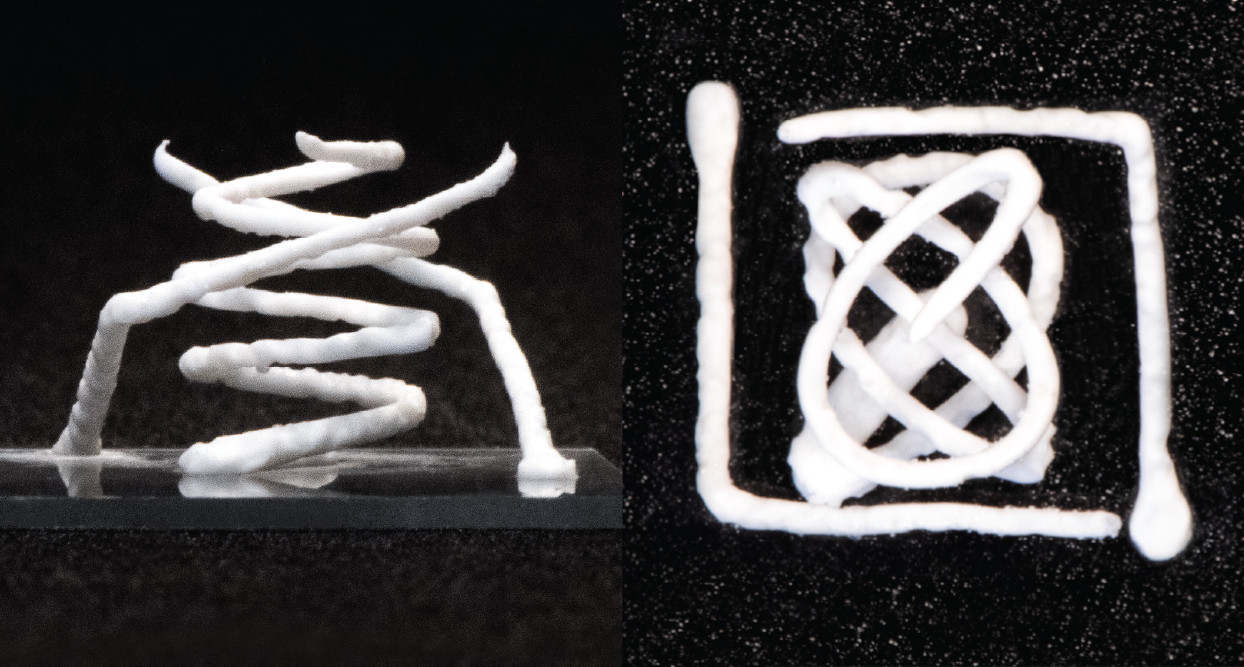
This 3D-printed glass has the potential to displace plastics widely used for 3D printing, and can improve the ruggedness and recyclability of electronic components. Achieving optical clarity is the biggest remaining challenge for this technology to enable its use in optical systems. Creating optics is difficult, and the surface of the optics must have the ideal roughness for high-performance optical systems such as high-performance sensors or fiber optic lasers.
This project is one of many 3D-printing materials being developed by the research group. The team is also working to make the material suitable for use in cleanroom environments by removing sodium from the material, because sodium can interfere with microelectronics. If successful, the technology could help further other research and development projects underway at the Laboratory, such as creating integrated circuits for 5G applications.
Inquiries: contact Kylie Foy