Liquid crystal device could allow for fast and reliable laser-beam steering
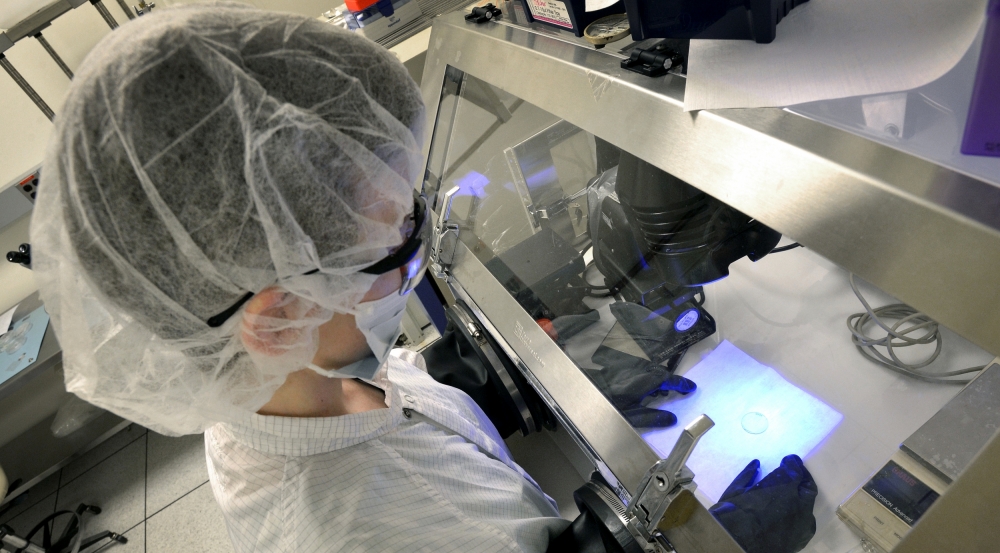
Many innovative technologies developed at MIT Lincoln Laboratory involve steering laser beams to create maps from afar, enhance space communications, or conduct surveillance of ground sites. All current devices used to steer these beams, including gimbals and turrets, are mechanical. These mechanical systems are highly capable but have drawbacks: the higher the performance (accuracy, speed, and aperture size), the greater the mass of the system. The weight of these systems can range from 13 pounds to 250 pounds or more. While these large mechanical systems work, researchers at Lincoln Laboratory and Kent State University's Liquid Crystal Institute are exploring a new option to steer laser beams used by systems integrated on increasingly compact aircraft and satellites. Liquid crystal polarization gratings (LCPGs), also called Pancharatnam phase devices (PPDs), provide desired capabilities, such as light weight, large aperture, wide steering angles, low loss of laser power, and fast switching speed to aim the beam; however, these LCPG beam-steering devices are not yet widely commercially available or fully characterized for demanding applications.
"These thin-film devices could potentially make laser-based sensors like lidar a lot lighter weight and more agile than current systems and, in turn, could make for new ways of using those sensors like frequently revisiting points of interest rather than scanning a fixed pattern," said Joseph Vornehm, one of the Lincoln Laboratory researchers on the project. "We’re excited to push the boundaries of this technology and understand what the possibilities and limitations are and how those translate into mission opportunities for potential sponsors."
Vornehm, Harold Payson, Shaun Berry, Valerie Finnemeyer, and Brian Roberts from Lincoln Laboratory, along with Kun Gao, Colin McGinty, and Philip Bos from Kent State University, have worked to improve the LCPGs for efficiently steering beams to high angles. The research team is now seeking to combine multiple LCPGs into a full beam-steering system that enables continuous steering instead of pointing the laser at discrete angles. They will present their work at the American Institute of Aeronautics and Astronautics DEFENSE Forum on 25 April 2017 in Maryland.
The LCPG/PPD is composed of a glass substrate, an alignment layer, and multiple layers of a liquid crystal known as RM257, which are polymerized to lock in the desired optical pattern. The fabrication process begins when a dye called Brilliant Yellow (BY) is dissolved into a dimethylformamide solution, which is applied onto a glass disc and then dried in an oven. The BY layer is the alignment layer and is photosensitive, i.e., reactive to light. Once the alignment layer has hardened, the device is exposed to two polarizations of laser beams: right-handed circular polarization (RCP) and left-handed circular polarization (LCP). This exposure is known as a holographic writing process. During this process, the BY molecules align in such a way that when RCP light is directed at the device, LCP light comes out at the same angle at which the LCP light was first exposed to the device.
The alignment layer is the blueprint for the liquid crystal layers. When a liquid crystal layer is spin-coated on top of the alignment layer, the crystal molecules self-align with the BY molecules, replicating the pattern that the polarized light created in the alignment layer. The thin liquid crystal layer must be solidified in this configuration before more layers can be added. To harden the device, it is exposed to ultraviolet light, which triggers a polymerization reaction to bond the liquid crystal molecules and secure them in place. Typically 10 to 15 layers of RM257 liquid crystal are added and polymerized until the device reaches the maximum steering efficiency for the desired optical wavelength. Maximum steering efficiency occurs when the laser beam loses the least amount of power when being steered through the device.
Although one device will only allow the laser beam to be pointed at two different angles (e.g., left by 25° for left-handed polarized light input, right by 25° for right-handed input), the devices fabricated at different streering angles can be stacked to create a range of steering angles. Between each LCPG sit polarization-switching elements that control the beam’s path through the steering elements and determine its final steering angle. Fine angle adjustments can then be done by adding a small, low-mass, fast-steering mirror behind the LCPG stack to fill in the small gaps between the LCPG stack angles.
These liquid crystal devices maintain a high efficiency of laser-power throughput, reliably put laser light on a target, support the beam to aim at long-range targets without a loss of performance, have low light leakage in unwanted directions, are able to switch between pointing angles quickly, and are much lighter than current laser-beam-steering systems. Lincoln Laboratory has developed many technologies that use laser-beam steering including systems that can detect activity in heavily foliated areas, download and upload data from satellites to Earth, and produce high-resolution, 3D renderings of terrain and infrastructure. All of these technologies require precise, reliable laser-beam pointing that could benefit from the development of high-speed, low mass liquid crystal beamsteering devices.