Low-Temperature Additive Manufacturing of Glass

Additive manufacturing (3D printing) holds promise for fabricating complex glass structures that would be unattainable with traditional glass manufacturing techniques. Lincoln Laboratory’s innovative approach allows additive manufacturing of multimaterial glass items without the need for costly high-temperature processing techniques. Our low-temperature technique could facilitate the widespread adoption of 3D printing for glass devices such as microfluidic systems, free-form optical lenses or fiber, and high-temperature electronic components.
KEY FEATURES
-
Via direct ink writing, Lincoln Laboratory uses custom inks from a variety of inorganic materials combined with a silicate solution to engineer the optical, chemical, and electrical properties of a composite
-
The ink ingredients are widely available, and direct ink writing affords a broad range of geometric freedom for creating glass structures
-
The curing process generates a stable glass structure requiring only a 250°C heat treatment instead of typical glass processing at temperatures > 1,000°C
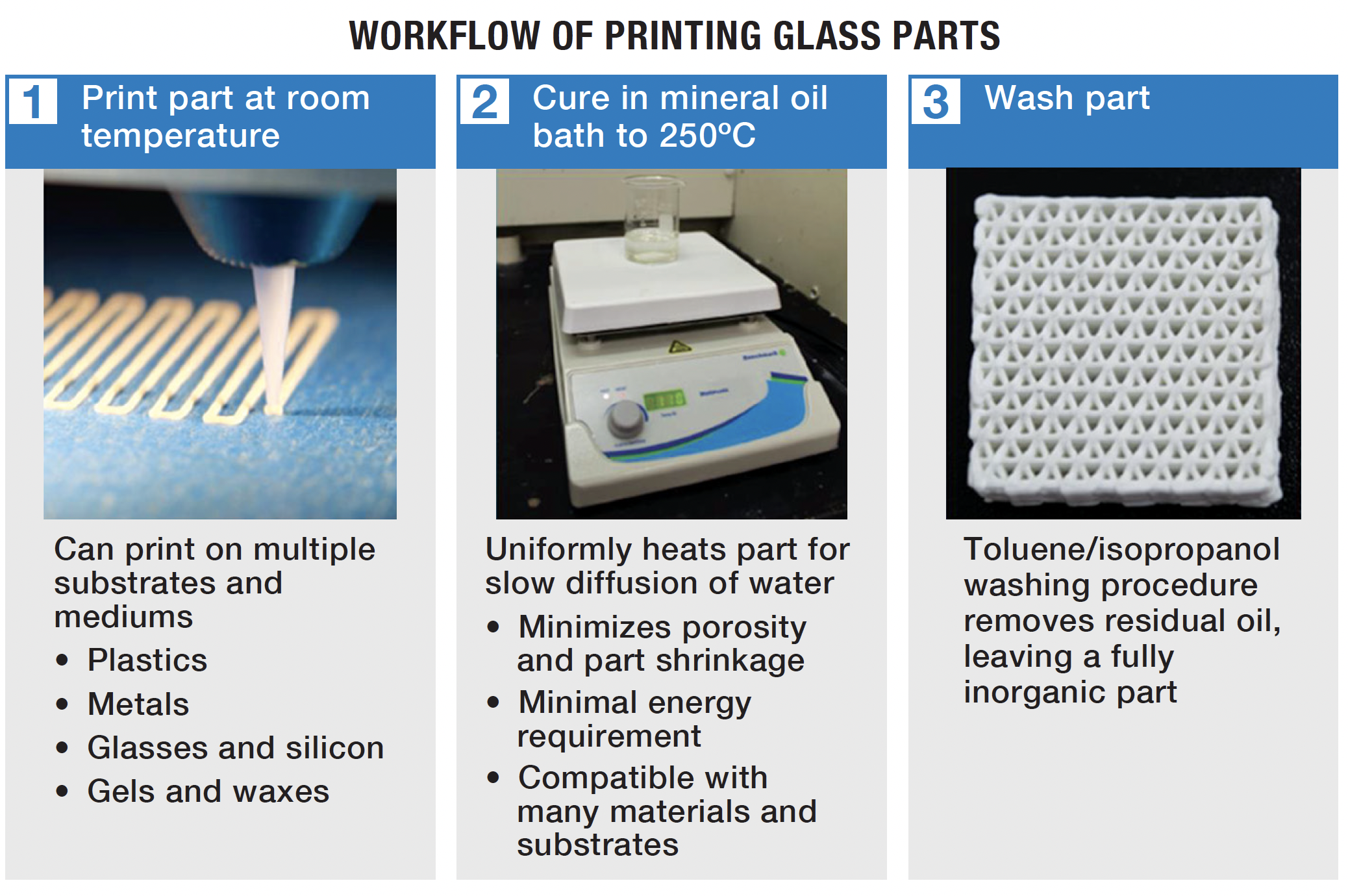
Additive manufacturing has expanded the ability to rapidly and cost-effectively create system components. However, traditional materials — various plastic and metal composites — can produce 3D printed structures with mechanical, chemical, and thermal instabilities. Using inorganic composite glasses solves many of the instability issues and offers a promising approach to create structures with diverse shapes and properties. However, the high temperatures (greater than 1,000°C) typically used to sinter (harden) glass items have hindered the use of glass in 3D printing. High-temperature processing requires specialized equipment and is incompatible with temperature-sensitive materials and components.
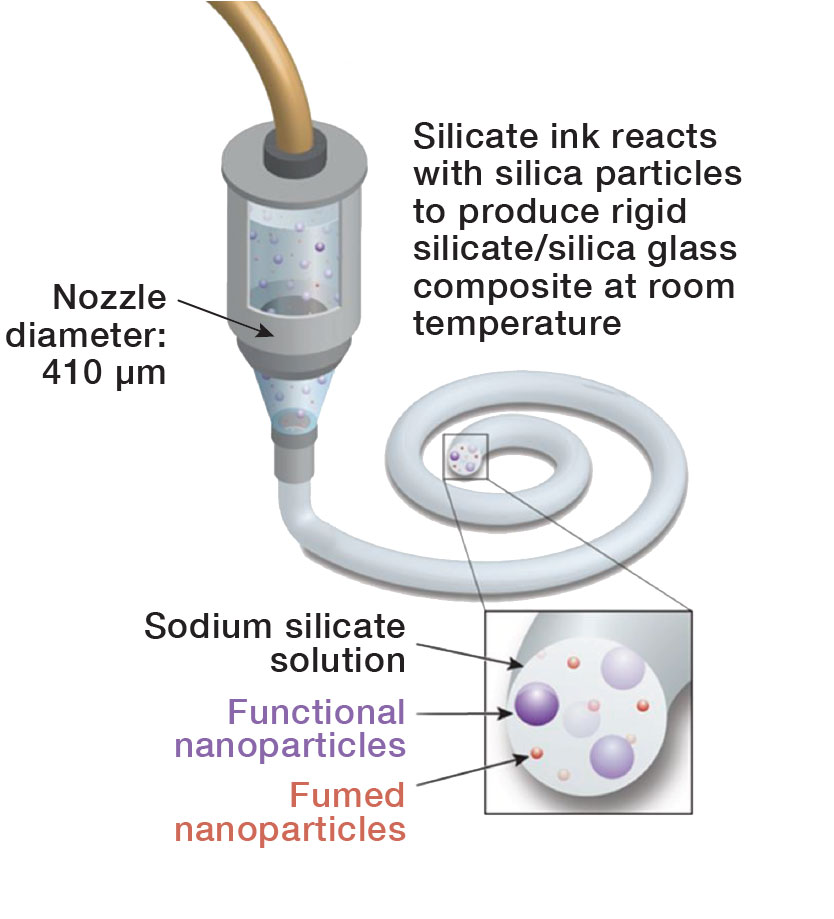
Lincoln Laboratory has demonstrated viable low-temperature 3D printing of glass structures. The process uses the direct ink writing technique to extrude, layer by layer, the Laboratory-developed multimaterial glass ink (composed of a silicate solution and nanoparticles of other inorganics) into the desired form. The process is done at room temperature. To ensure structural stability, the item is cured in a mineral oil bath heated to just 250°C. Following heat treatment, the structure is rinsed in an organic solvent to remove residual mineral, leaving a fully inorganic silica item.
Tests on items built via low-temperature additive manufacturing have shown promising results:
- Structures with a high degree of resolution
- High thermal stability
- Minimal shrinkage
Ongoing research is focused on improving the optical clarity of the glass and creating inks that enable different chemical and electrical properties.