Microhydraulic Actuator Development

Lincoln Laboratory is developing microhydraulic actuators, a new class of actuating material that is composed of layers of thin sheets separated by structured fluids. By integrating surface tension forces between the sheets, actuators move as the sheets slide relative to each other.
KEY FEATURES
- New type of actuation based on solid and fluid components working together
- Highly efficient and powerful, with 60% efficiency and demonstrated power density similar to biological muscle
- Highly scalable, with power density 100× that of muscle for scaled systems
- 3D scalable to macroscopic sizes
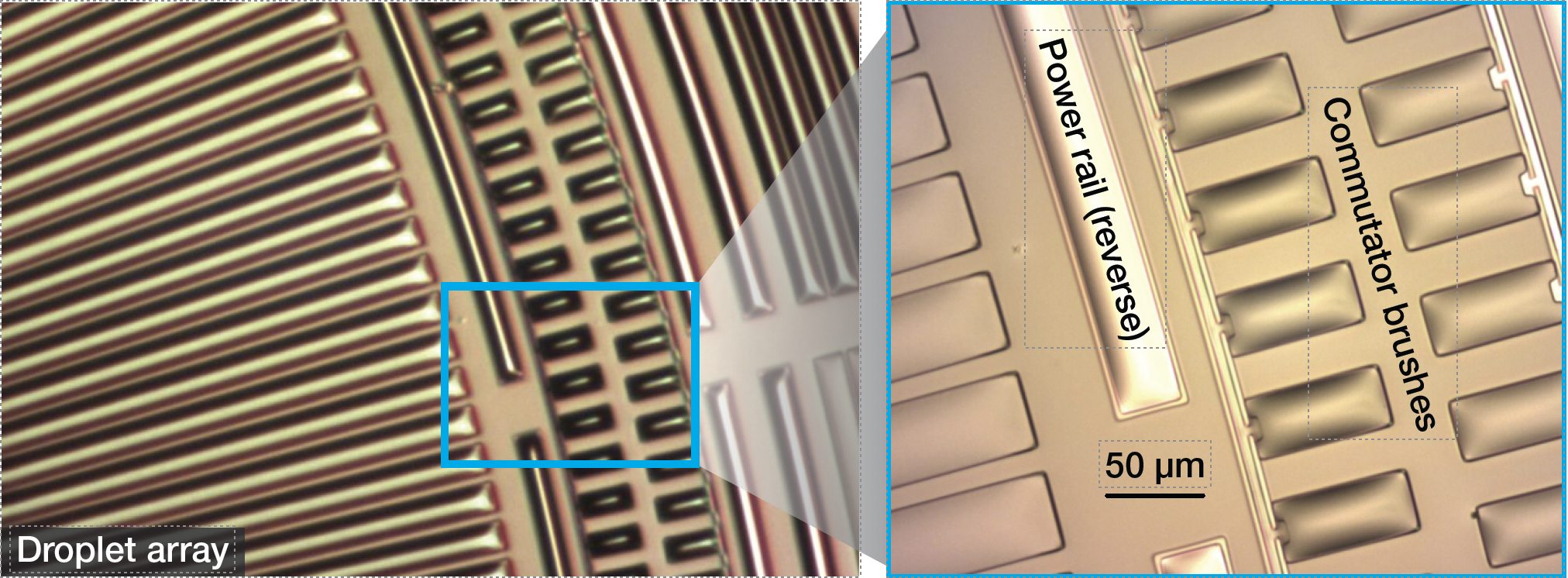
Microhydraulic Actuator Operation
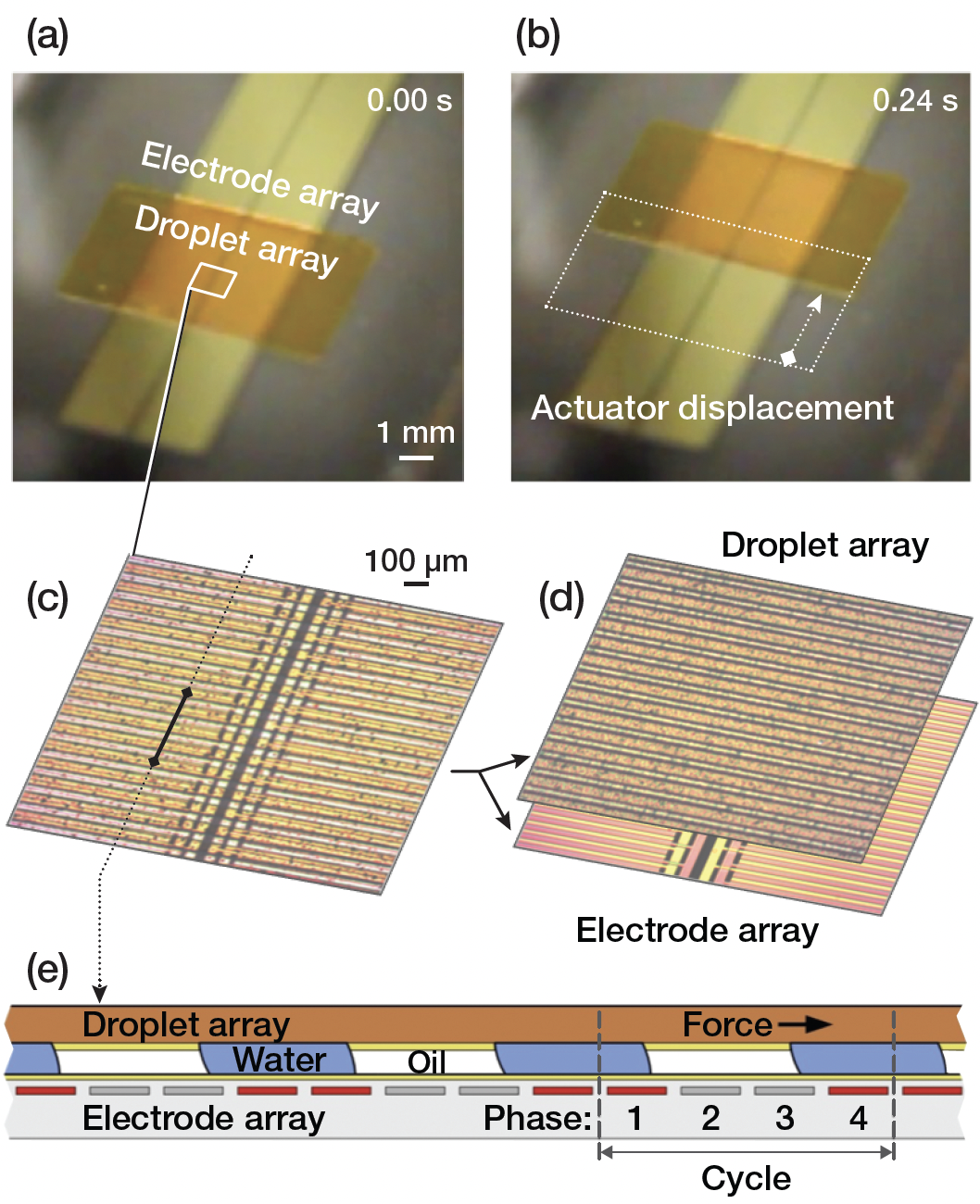
(a) A proof-of-concept linear actuator showing the base electrode array and the rectangular polyimide droplet array riding on top. The two arrays are separated by a thin ~15 µm layer of fluid composed of water miscible droplets and surrounded by oil. The water droplets are attached to the droplet array by patterned hydro-philic regions, but are free to slide on the hydrophobic electrode array when the electrodes are off.
(b) The droplet array is displacing by 3 mm in 0.24 s, after 30 cycles of actuation.
(c) A magnified top-down view of the actuator.
(d) Separate images of the two arrays.
(e) A cross-section view of the actuator during operation. The electrode array consists of electrodes repeated in cycles; in this design, there are 4 electrode phases per cycle. During operation electrodes are sequentially turned on, pulling the drops and the droplet array by electrowetting action. In the current step the red electrodes (1, 4) are on, in the subsequent steps electrodes (1, 2), then (2, 3), then (3, 4) will be on, until the cycle returns to (1, 4).
Potential Applications
- Actuators for efficient and scaled micro-robotics
- Artificial muscle-like material for flight control surfaces on unmanned aerial vehicle, exoskeleton, and artificial limb systems
- Micromotors and shape-change materials for scaled optical systems, such as gimbals, adaptive optics, and beam-steering systems